Residual & Distillate Fuels Analysis
according to ISO 8217
The International Standards Organization (ISO), in collaboration with shipowners, shipping associations, national standardization bodies, classification societies and the general petroleum industry, compiled ISO 8217: 2017. The growing demands of environmental legislation lead to a shift in the nature of marine fuels including petroleum products that contain products from renewable or alternative sources. This model, taking into account the different fuel nature, incorporates all categories of distillate and residual fuels despite the fact that several of these categories are not available at all sites.
ISO 8217: 2017 specifies the requirements for 7 categories of distillation fuels and 6 residual fuels as presented in Table I and Table II.
Melco Labs is able to provide their customers with the complete set of analyses for their product classification.
Kinematic Viscosity
Kinematic viscosity is the most important characteristic for the classification of fuels.
KV values are essential for the correct onboard use of the fuel.
When the fuel's KV does not meet the manufacturer's specifications, incomplete combustion, deposit formation and energy losses may occur.
​

Sulphur

When fuel is burnt, the sulfur content is converted to sulfur oxides. Sulfur oxides are corrosive to the mechanical parts of the ship and are neutralized by the alkalinity of the lubricants used.
If the right lubricant is used, the sulfur content is of minor importance, but it can have environmental impact for which new regulations are about to be implemented (IMO 2020).
Acid Number
High acid number fuels can cause malfunctions to the vessel engine, especially in the injection system and the fuel pump.
TAN test i.a.w. ASTM D 664 evaluates the presence of acid substances in the fuel.

Micro Carbon Residue
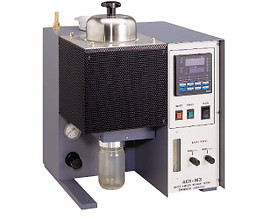
Carbon residue is determined by a laboratory test performed under specified reduced air supply. It does not represent combustion conditions in an engine.
It gives an indication of the amount of hydrocarbons in
the fuel which have difficult combustion characteristics.
The micro carbon residue method is specified by ISO 8217.
Density
Density is important for calculating the quantity of fuel during deliveries and is also essential for onboard fuel handling.
Density, combined with viscosity, are used to calculate the Calculated Carbon Aromaticity Index (CCAI), which is indicative of the ignition characteristics of residual fuels.
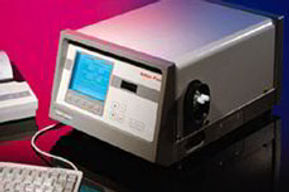
Elements - ULO
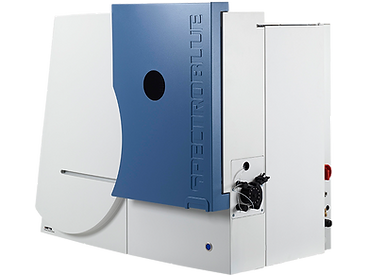
Elements
Vanadium, Nickel and Sodium are common constituents of heavy fuels. When burned, oxides are produced that can end up as deposits, causing wear in the mechanical parts of the ship.
Used Lubricating Oils (ULO)
The presence of zinc, phosphorus and calcium in residual fuels above the limits set in table II, indicates contamination of the fuel by ULO.
Flash Point
The flash point of all fuels other than the DMX class is set at a minimum of 60 °C according to SOLAS guidelines. Flash point value is essential for storage conditions and personnel safety.
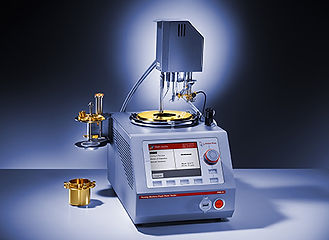

Pour Point/Cloud Point/CFPP
These tests are indicative of the paraffin content of the fuel and thus its low temperature behaviour. Depending on the trip and the equipment used, the handling of the fuel is planned accordingly.
Cat Fines Al+Si
Aluminum and silicon are elements that originate from the degradation of the catalyst (aluminum silicate) used in the refinery during catalytic cracking. These components can not be removed entirely from the fuel, resulting in the risk of erosion of pumps, injection systems and cylinders. ISO 8217: 2017 sets the acceptable Al + Si values based on the IP 501 method.
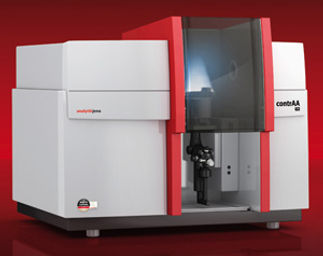
Water Content
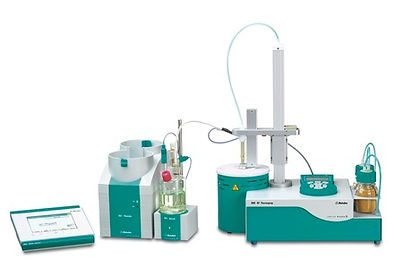
Water in the fuel as a contaminant can be removed onboard by centrifugation. High concentrations of water can result to insufficient combustion and risk of pumps cavitation. Remaining water in the pipelines for long periods of time causes corrosion.
Total Sediment
The greatest risk of sediment formation in heavy fuels is due to a possible coagulation of organic material inherent in the fuel itself. Asphaltenes can form precipitates (setting is affected by time and temperature). The T.S.P (total sediment potential) test with aging provides information about the amount of sediment that can be formed under normal storage conditions, excluding external influences. If the total sediment exceeds the specification (maximum 0.10% m/m), problems with the fuel cleaning system and the filters may occur.
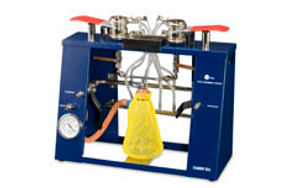
Ash
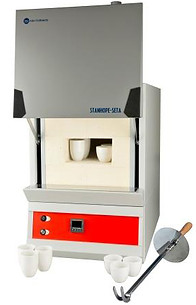
All residual fuels contain metals, either naturally occurring in crude oil such as vanadium, sodium, calcium and nickel, or are imported from external sources such as sodium, aluminum, silicon, potassium and iron. When the fuel is burned, some of these metals are converted into solid particles of oxides, sulphates or more complex compounds, commonly known as ash. At certain temperatures, these solid ash particles become partially fluid and, in this condition, can adhere to the surfaces of the metal parts of the equipment if the temperatures are quite high. These ash deposits can damage the mechanical components of the ship.
The temperature at which ash particles begin to become fluid with the risk of sticking to the surfaces is often referred to as a "contraction" temperature and is lower for ash and / or sodium rich ash.
This is why particular attention is paid to the quantities of these metals in fuels.
A 1:3 sodium / vanadium ratio generally claims to give the lowest ash melting temperature.
Cetane Index
Cetane index is only applicable for gasoil and distillate fuels. It is a measure of the ignition quality of the fuel in a diesel engine. The higher the rpm of the engine, the higher the required cetane index. The cetane index is an approximate calculated value of the cetane number, based on the density and the distillation of the fuel. The cetane index is not applicable when cetane-improving additives have been used.
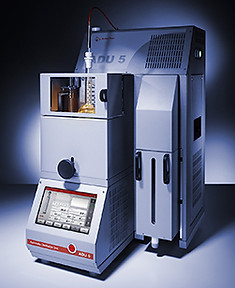
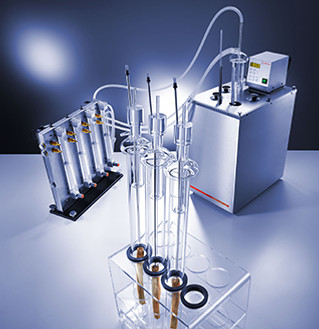
Oxidation Stability
Degradation of distillate fuels by oxidation can cause fuel stability problems. Unstable distillate fuels can form insoluble organic particles which may clog fuel filters, cause wear and contribute to injector deposits.
Current supply logistics make it almost inevitable that marine distillate fuels can contain bio-derived material, i.e., fatty acid methyl esters (FAME), that can impact the oxidation stability of the fuel.
Lubricity
Using the High-Frequency Reciprocating Rig (HFRR), the lubricating property in diesel fuels is assessed. Lack of lubricity in diesel fuels can cause wear to the equipment due to excessive friction and can shorten the life of engine components.
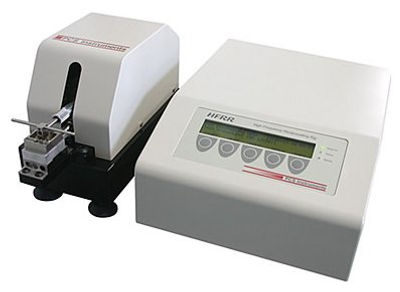
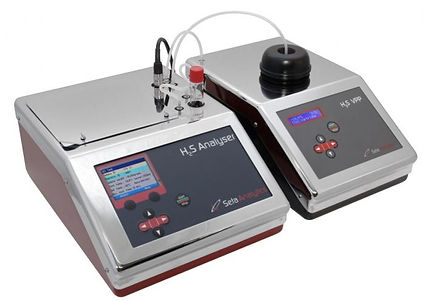
Hydrogen Sulphide
Hydrogen sulfide (H2S) is a highly toxic gas. Exposure to high vapour concentrations is hazardous and in extreme cases, can be fatal.
H2S can be formed during the refining process and may evolve from the fuels in storage tanks, in product barges and customer tanks.
Hydrogen sulphide in high concentrations in bunker fuels can create corrosion in the ships engines and safety hazards for land based storage installations. The current specifications of marine fuels dictates that the allowed limit for hydrogen sulphide concentration is 2 parts per million only.
FAME
Environmental needs for reducing greenhouse gases and sulfur emissions (SOx) lead to the use of biofuels and blends of biofuels with petroleum products.
Fatty Acid Methyl Esters (FAME), also known as biodiesel, is produced from vegetable oils, animal fats or waste cooking oils by transesterification.
Although biodiesel has good combustion, lubrication and natural environmental benefits, it has problems with its storage and management and that is why there are limits in its use as a low-blend component in transport fuel (up to 7% in Europe according to EN 590).
​
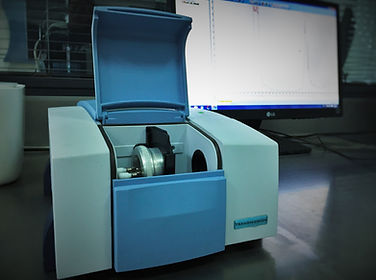